Engineers at Duke University have made a groundbreaking discovery that could help reduce the environmental footprint and human health risks of the electronics industry.
In a new study published in the journal Nano Letters, they’ve developed the world’s first fully recyclable printed electronics that use water instead of hazardous chemicals in the fabrication process.
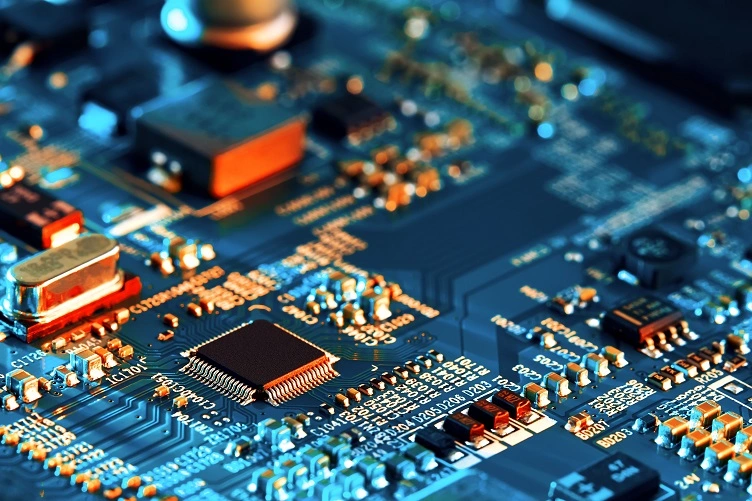
Challenges of Printed Electronics in Manufacturing
One of the biggest challenges facing the electronics manufacturing industry is successfully securing multiple layers of components on top of each other to create complex devices. This can be a frustrating process, particularly for printed electronics.
Carbon-Based Inks
In previous work, Franklin and his group demonstrated the first fully recyclable printed electronics using three carbon-based inks: semiconducting carbon nanotubes, conductive graphene, and insulating nano-cellulose. However, when attempting to adapt the process to use only water, the carbon nanotubes presented a significant challenge.
Water-Based Ink
To create a water-based ink in which the carbon nanotubes don’t clump together and spread evenly on a surface, a surfactant similar to detergent is added. However, the resulting ink doesn’t create a layer of carbon nanotubes dense enough for a high current of electrons to travel across.
Recyclable Water-Based Transistors
To achieve their breakthrough, Franklin and his team developed a unique, cyclical process that involves rinsing the device with water, drying it in low heat, and then printing on it again.
This process eliminates the need for harsh chemicals or high temperatures typically used to remove surfactants in traditional manufacturing processes. By reducing the amount of surfactant used in the ink, Franklin and his team were able to create fully functional, fully recyclable, and water-based transistors.
Their innovative process presents a new approach to electronic manufacturing that significantly reduces environmental footprints and human health risks. Not only does their technology reduce waste, but it also uses less water than traditional fabrication methods that rely on toxic chemicals.
With this breakthrough, the team hopes to inspire more research into making electronic manufacturing processes much more environmentally friendly.
Viable Path Toward Environmentally-Friendly Manufacturing
Compared to a resistor or capacitor, a transistor is a relatively complex component used in devices such as power control or logic circuits and sensors.
Franklin hopes that by demonstrating a transistor first, he can signal to the rest of the field that there is a viable path toward making some electronics manufacturing processes much more environmentally friendly.
Reducing Electronic Waste
According to a United Nations estimate, less than a quarter of the millions of pounds of electronics thrown away each year are recycled. As the world eventually upgrades to 6G devices and the Internet of Things (IoT) continues to expand, this problem is only going to get worse.
Therefore, any dent that could be made in this growing mountain of electronic waste is important to pursue.
Future Applications of Printed Electronics
While more work needs to be done, Franklin believes that this approach could be used in the manufacturing of other electronic components like the screens and displays that are now ubiquitous to society.
The current fabrication technology is high-energy and relies on hazardous chemicals as well as toxic gases. The entire industry has been flagged for immediate attention by the US Environmental Protection Agency.
Competitive Results
Although the performance of the thin-film transistors developed in the study doesn’t match the best currently being manufactured, they’re competitive enough to show the research community that more work should be done to make these processes more environmentally friendly.
Check out this other article we explore Innovative Solutions For A More Resilient Future.
Conclusion
Currently, electronics are produced using traditional manufacturing processes that rely heavily on the use of hazardous chemicals and high-energy processes that pose significant human and environmental health risks.
These processes require large amounts of water and energy to produce electronic devices and their components, and the resulting waste and environmental impact are significant.
By contrast, the new solution developed by Franklin and his team at Duke University uses water instead of chemicals to produce fully recyclable printed electronics.
This approach significantly reduces the environmental footprint of electronics manufacturing and eliminates the need for harsh chemicals and toxic gasses, making the process much more environmentally friendly.
Reference
Fully recyclable printed electronics ditch toxic chemicals for water. (2023, April 6). Link to the source